PVD coating
What is PVD coating?
PVD coatings are extremely thin coatings (0.5 – 5 μm) produced by modern vapor deposition technology in a vacuum. Thin coatings produced in such an environment are always characterized by significant improvement of various properties:
- The surface hardness is increased to such values that are unattainable even for the hardest steels. Therefore, most PVD coatings are very scratch resistant and durable.
- Higher chemical stability and thus significant increase in corrosion resistance in various environments (moisture, acid, oxidation).
- Significantly lower wear due to reduction of the coefficient of friction.
- Adjustability of product appearance through a wide range of uniform coating colors.
- A strong bonding force between the coating and the substrate can be achieved on a wide range of materials.
- The coatings are harmless to the human body and the environment.
High-quality coatings characterized by the above-mentioned properties are our core service under the specific label deQoline®.
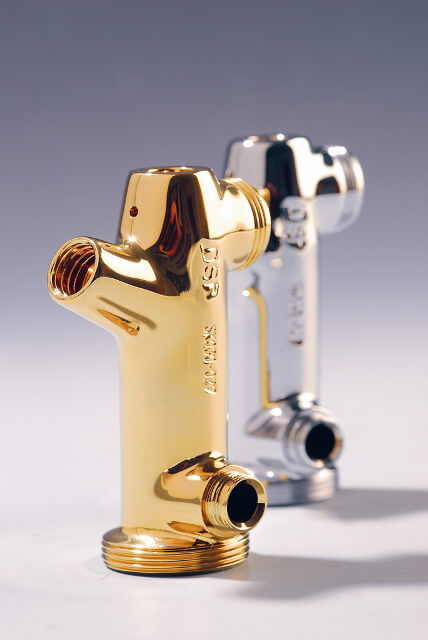
deQoline®
deQoline® includes numerous coatings developed and produced by TECHNO-COAT. All our coatings and their production processes are carefully defined by our quality management system to ensure the best possible repeatability and results of the coatings produced.


Coating | Color | deQoline® |
---|---|---|
TiN | Gold, Nickel, Steel | D, N |
TiCN | Copper, bronze, anthracite | B |
TiAlN | Black, Anthracite | C |
ZrN | Light yellow, nickel, steel | A, N |
ZrCN | Brass | A |
CrN | electroplated chrome | H |
DLC | Anthracite | DLC |
How does PVD coating work?

PVD coating is a modern and environmentally friendly process for the production of thin layers based on vacuum technology. The main players in this process are clean metal solids (“targets”) such as titanium, zirconium, chromium and other metal elements. These “targets” are vaporized in two possible ways (“sputtering” or “arc discharge”) and the ions of the target material are directed to the products surrounded by the plasma of the reactive gas (usually nitrogen). The chemical reaction between the metal ions and the reactive gas leads to a steady nano-formation of the thin coating, which is characterized by excellent mechanical, chemical and optical properties.
A major advantage of PVD technology is that it is carried out at very low temperatures (below 250 °C). This is extremely positive for steel materials, as the PVD process temperatures are far below the usual heat treatment temperatures and the core microstructure and mechanical properties of the substrate material remain unchanged!
Our 30 years of experience and fundamental understanding of the physical processes behind coating formation have led us to develop many different types of coatings. Slight variations in process parameters and coating composition allow our customers to choose from a huge palette of available colors, ranging from gold-like yellow to deepest black.
Which materials can be PVD coated?

The following materials are suitable for PVD coating:
- All steel families, especially high-alloy steels such as high-speed steels and stainless steels
- Hard metals and other tool materials
- Non-ferrous metals such as copper and aluminum and their corresponding alloys (e.g. brass)
- Chrome or nickel plated metal products
Important to know: Brass without galvanization or galvanized materials are very vacuum-unfriendly! The reason is that elements such as zinc and lead can easily evaporate in the vacuum environment and negatively affect the production process and the vacuum stability of the furnace!
Are you looking for a partner for PVD coatings?
Then contact us now. We look forward to being able to process your request individually.
What to consider?
Four important production factors of PVD technology are to be considered:
- Line-of-sight transfer is typical of most PVD coating techniques. It is important to note that closed surfaces/holes cannot be coated.
- The coating produced follows the original surface morphology of the product and is therefore highly dependent on the surface pretreatment. A polished surface always shows the best aesthetic results.
- A great deal of attention must be paid to surface cleanliness, as even the smallest particles of dirt and fingerprints can have a negative impact on the final result. The product of each customer is thoroughly cleaned at TECHNO-COAT, but it is preferred that the customer also has the awareness of the importance of cleanliness.
- Tightly sealed tapped holes are a potential problem during production, as trapped air can leave the hole during vacuum deposition, and the presence of oxygen can negatively affect the quality and optical properties of the coating. To ensure the best quality of the coating, it is recommended to avoid closed cavities on the product in the PVD production phase.