Burnishing
What is burnishing?
Burnishing is a process for surface finishing of ferrous materials.
In contrast to the PVD process, black oxidation involves a chemical transformation of the surface.
The iron present in the steel reacts chemically with the oxygen in the process solution to form a noble oxide.
Burnishing technology originally gained popularity in the weapons industry as it gives firearms a black appearance and improved corrosion protection.
These positive properties have led to black oxidation also gaining a foothold in other areas, for example in the mechanical engineering industry.
The surface has a columnar structure and forms small gaps in which oils and other lubricants can be deposited.
This reduces sliding friction.
The characteristic structure of the coating has only a negligible effect on the dimensional accuracy of the components.
Advantages of burnishing
- Excellent sliding properties, due to depot formation
- Very thin layer, which is not applied from the outside but grows out of the base material
- Layer distribution is uniformly low (approx. 1 µm) - therefore ideal for fits
- Gives the finished part an attractive black look
- Temporary increase in corrosion protection (defined by post-treatment)

How does the burnishing work?

Coarse impurities and corrosion products are removed from the workpieces by boil-off degreasing and pickling to create a basis for further finishing.
The hot black oxidizing process (DIN 50938) produces a deep black and dimensionally stable oxide layer on ferrous products, depending on the base material.
The products are immersed in highly concentrated alkaline molten salts at temperatures of up to 140 °C.
After treatment, the components are rinsed several times to remove the molten salt from the workpiece.
The burnished surface is then dewatered and lightly oiled using a dewatering fluid.
Post-treatment according to DIN 50938
Designation | Type of follow-up treatment | Corrosion protection | Field of application |
---|---|---|---|
T0 | No follow-up treatment | temporary - minor | Mechanical engineering, decorative sector |
T10 | Water-displacing corrosion inhibitors | temporary - recommended | Mechanical engineering, decorative sector |
Are you looking for a partner for burnishing?
Contact us now. We look forward to dealing with your request individually.
Why with Techno-Coat?
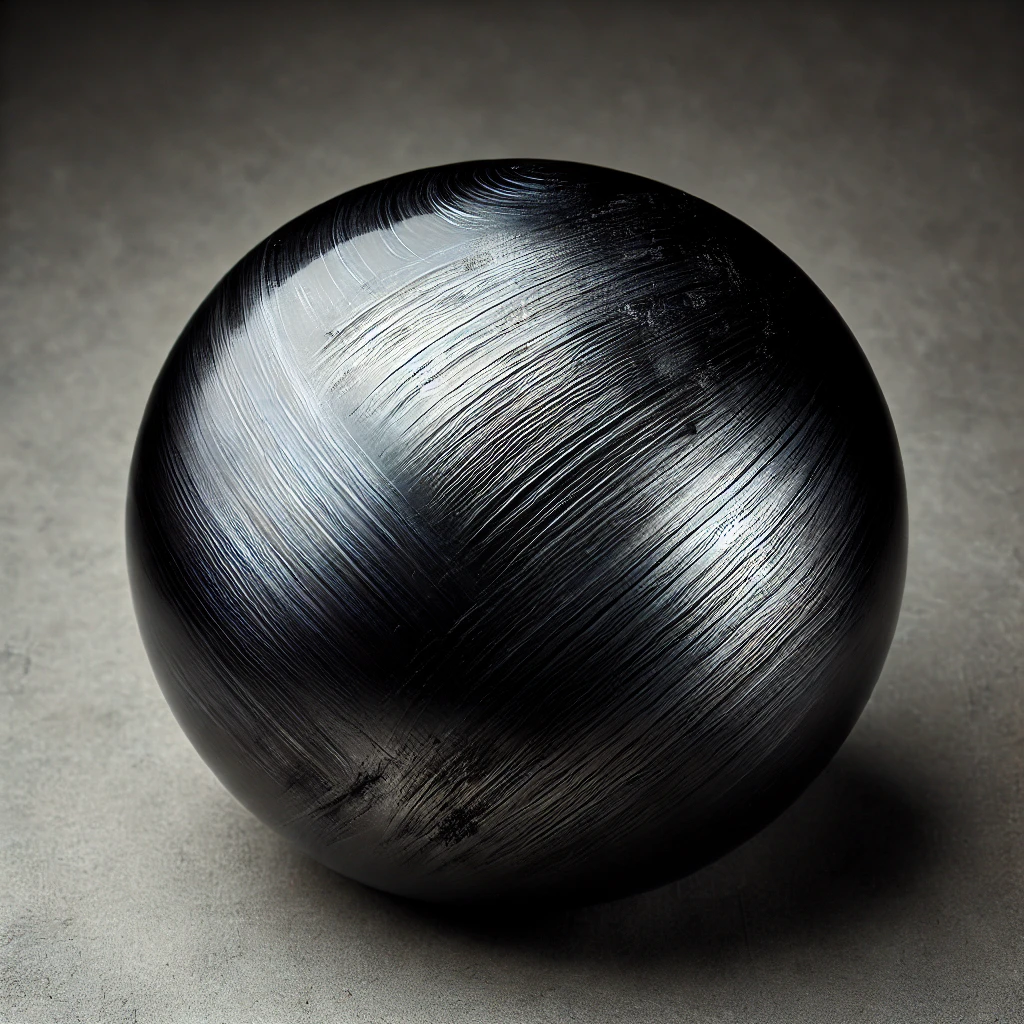
Everything from a single source
Burnishing is just one of our many areas of expertise in surface finishing. We offer you a range of other processes, such as PVD, electroplating or stainless steel blackening.
Speed
Speed in responding to enquiries and in processing orders has distinguished us for many years.
Many years of experience
Our entire experience from over 25 years of surface coating also flows into the black finishing of your products.
High quality standards
Finishing your products to the highest quality standards is our top priority. Internal testing procedures and our QMS in accordance with DIN ISO 9001 guarantee this in the long term.
How we burnish - the process
Mechanical cleaning
As a pre-treatment, it may be necessary to remove scale, oxides and other foreign contaminants such as wax crayon, adhesive residues or paint from the components using suitable processes.
Decoction degreasing
Oils, fats and other additives are dissolved in the decoction degreaser and thus removed from the surface.
Sinks
Chemical residues from the degreasing process are removed in the rinsing tank.
This step is repeated several times during the rest of the process.
Pickling
A pickling process using phosphorus and sulphuric acid activates the surface and removes any oxides.
This is followed by a further rinse cycle.
Burnishing
The components are black oxidized in a 140 °C molten salt bath for 5 – 15 minutes.
This is followed by intensive rinsing cycles and finally a hot rinse cycle.
Dewatering Fluid
Finally, there is a dip in a low-viscosity fluid that displaces the water from the surface.
Would you like more information?
Then contact us now.
We look forward to being able to process your request individually.
Request now
Send us your request simply and conveniently using the form.
You will receive our information on the coating process directly afterwards.
If you are not sure about certain details, please contact us directly by e-mail or telephone or leave the fields blank.
We look forward to receiving your inquiry!
Your contact person
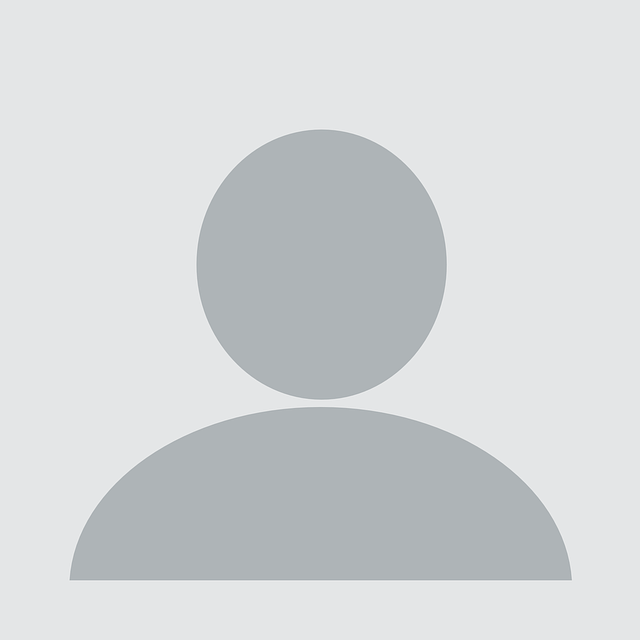
- Reiko Röthig
- r.roethig@techno-coat.com
- +49 (0) 3583 / 77 21 - 34
Frequently asked questions
The bluing offers the following advantages:
- Improvement of the sliding properties
- Uniform layer distribution
- Low layer thickness - geometry of the component remains unaffected
- Attractive black look
- Temporary increase in corrosion protection (depending on the post-treatment)
The following disadvantages must be taken into account when burnishing:
- Without post-treatment, burnished components are more susceptible to corrosion
- Cast components are given a reddish coating
- the quality of the resulting finishes is highly dependent on the nature of the base material (structure, mechanical processing, previous hardening processes)
All types of iron (cast iron, wrought iron, etc.) and common engineering steels are mainly suitable for burnishing.
Our system capacities are 600 x 300 x 400 mm. Please also contact us for oversizes.