Types of galvanization
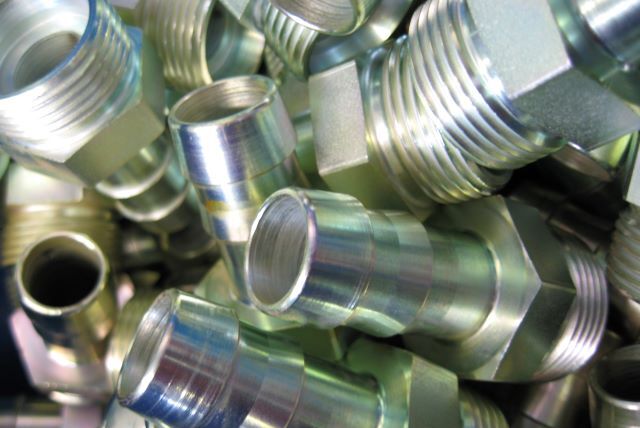
Galvanizing
Particularly suitable for decorative purposes in combination with high corrosion protection.

Chrome plating
Ideal base coat as it guarantees a hard surface and tarnish protection for nickel.
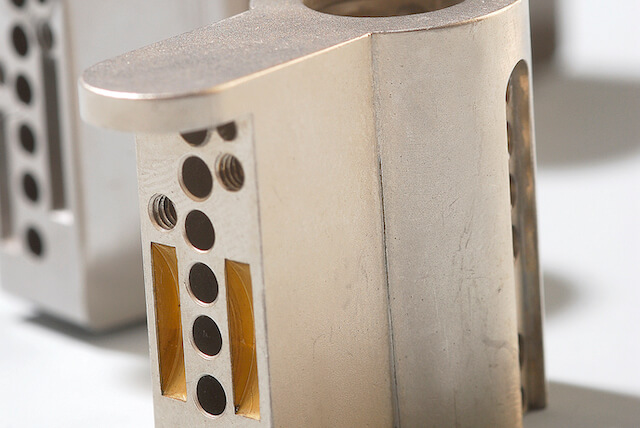
Nickel plating
Mainly used for corrosion protection of iron parts in various applications.
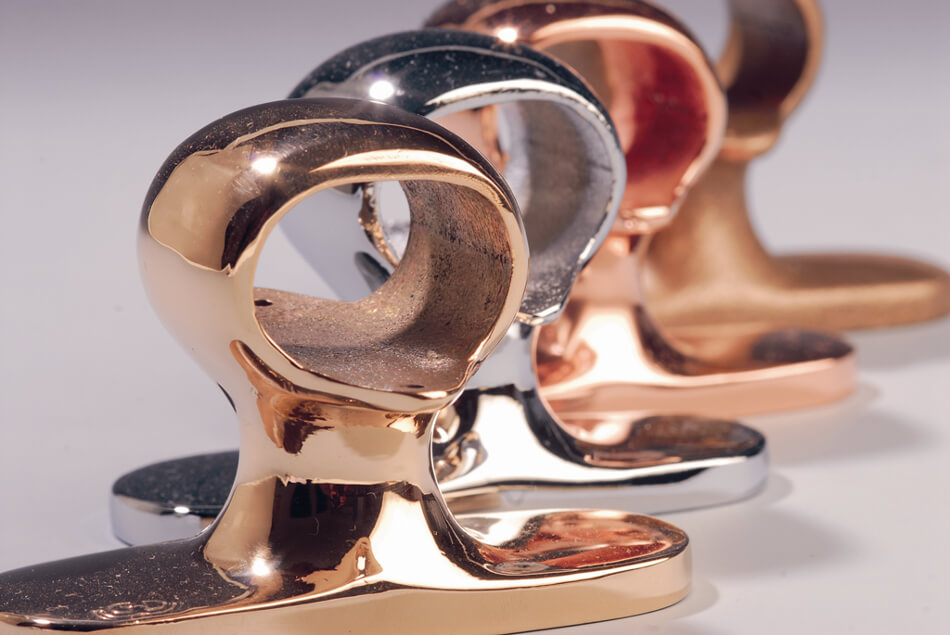
Copper plating
Suitable as an intermediate layer, it impresses with its adhesive strength and corrosion resistance.
What is electroplating?
Electroplating is a wet-chemical process for the deposition of metal. The anode material is dissolved with an electric current and deposited on the workpiece. There are countless electrolytes for a wide range of applications. You can have your products copper-plated, nickel-plated, chrome-plated or galvanized in our systems.
Advantages of electroplating
- Metallic feel and look for a particularly high-quality appearance
- Excellent corrosion protection of the coated surface
- Layer is resistant even at high temperatures
- Electrical conductivity of the base material is maintained or improved
- Post-processing (e.g. brushing) for other surface finishes possible
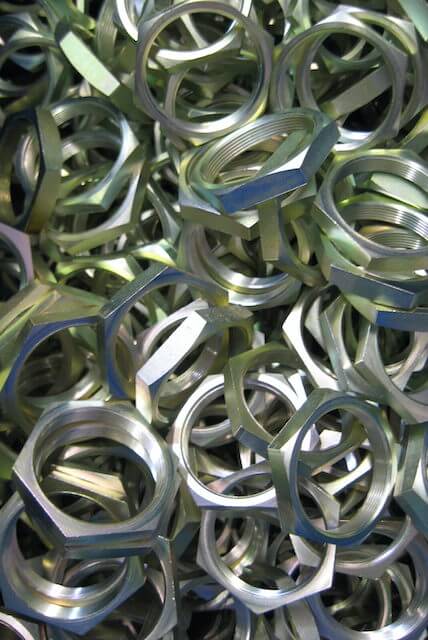
How does electroplating work?
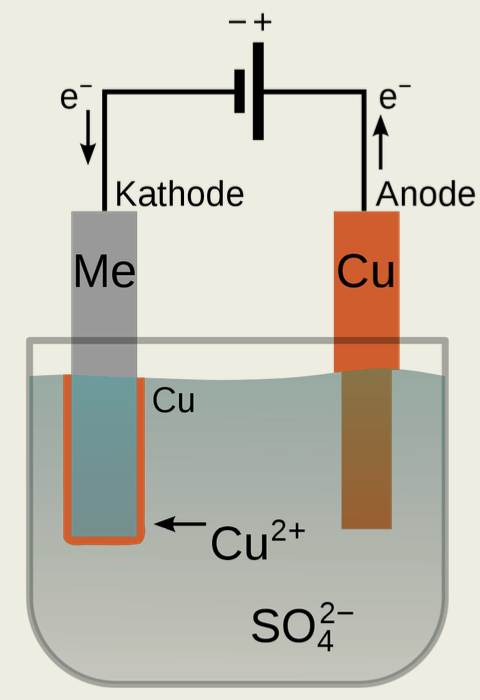
In electroplating, the component to be coated is immersed in an aqueous electrolyte containing metal. A charge exchange takes place that causes metal ions on the component to react to form solid metal.
This charge exchange can take place with the help of direct current or without current, i.e. without external current.
Electrolytes that deposit metal using direct current have soluble anodes (+) that consist of the pure metal that is to be deposited. The component is connected as a cathode (-).
Metal deposition without external current is carried out without additional current. The base material of the component is dissolved, leaving electrons on the workpiece.
These electrons reduce the metal ion present in the electrolyte, gradually building up a metal layer.
All components coated by us undergo several pre-treatments before the actual electroplating. Through chemical cleaning and degreasing processes, we can guarantee an excellent quality of the coating.
Are you looking for a partner for electroplated coatings?
Then contact us now.
We look forward to being able to process your request individually.
Where is galvanization applied?
There are hardly any limits to the possible applications. Galvanic processes are predominantly used for corrosion protection; in the automotive sector one can find some examples of this. Galvanic coatings are also very popular in the decorative sector. For example, furniture or door fittings and jewelry are often exposed to precious metals. Hard chrome is used as a technical layer for hydraulic cylinders, for example.
Mechanical and plant engineering
E.g. components for conveyor systems in the automotive industry, mining, etc.
Fastening technology and small parts
E.g. cap nuts, screw connections, nipples, hydraulic and compressed air fittings, etc.
Automotive and vehicle construction
E.g. hydraulic cylinders, brake callipers, remote control parts for caravans, etc.
Heating construction
E.g. pipe sections, connecting pieces etc.
Decorative applications
E.g. switch parts, fittings, ship parts, jewelry, etc.
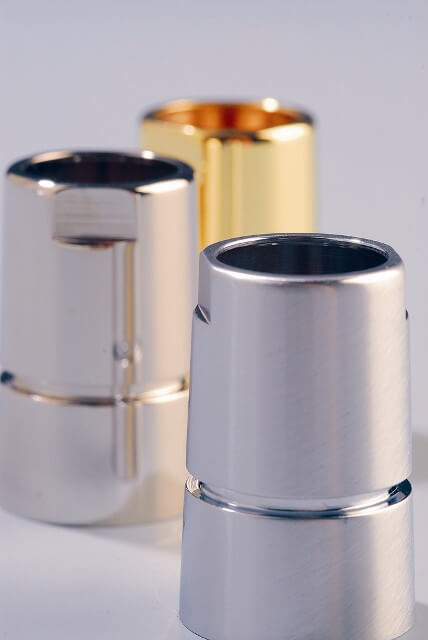
Frequently asked questions
What are the advantages of galvanizing?
Galvanic coatings are characterized by the following advantages:
- Metallic feel
- Metallic look
- high-quality appearance
- Very good protection against corrosion of all kinds
- Particularly temperature-resistant
- coated product remains electrically conductive or conductivity is improved
- Build-up of a plastic layer possible
- Post-processing of the surface possible
What are the disadvantages of electroplating?
The following disadvantages must be taken into account with electroplating:
- The design of the component must already be carried out in a coating-compatible manner during the planning phase
- Closed cavities should be avoided
- Components should not be welded together flat
- Chemical residues in welded constructions or assembled components can lead to corrosion
- Metal distribution is not uniform
- No precise details of the layer thickness in the μm range possible
- Unsuitable for fits and threads
- Nickel as a coating material can cause allergic reactions
How long do electroplated coatings last?
The durability of electroplating always depends on the respective area of application and the base material. With appropriate care and proper use, the coating will last for many years.
Which materials can be electroplated?
Many metals and their alloys can be electroplated, which requires different pre-treatment processes.
Plastic can also be electroplated, in which case a special treatment is required, as the prerequisite is an electrically conductive surface.
Is electroplating harmful to the environment?
Galvanic coating processes extend the service life of the coated parts. This means that replacement is only necessary after a long period of use. Electroplating therefore indirectly contributes to a better use of resources.
In addition, the waste water produced during the process is cleaned in our treatment plant before it is fed back into the cycle. We have been meeting the legal requirements and values in this area for years.
The exhaust air is also cleaned using water mist. This allows substances produced during the coating process to be filtered out.
Request now
Send us your request simply and conveniently using the form.
You will receive our information on the coating process directly afterwards.
If you are not sure about certain details, please contact us directly by e-mail or telephone or leave the fields blank.
We look forward to receiving your inquiry!
Your contact person
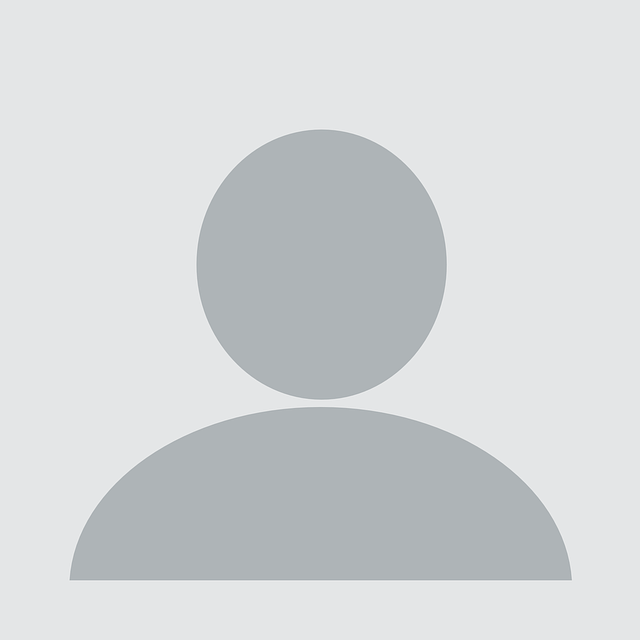
- Reiko Röthig
- r.roethig@techno-coat.com
- +49 (0) 3583 / 77 21 - 34